Beer bottling & canning solution
In the dynamic beer and beverage industry, the ongoing challenge is to boost productivity while cutting costs. With Hermann’s bottling/canning solutions, you can confidently enhance yield and minimize waste, making the right strides for success.
"Fostering Brewing Excellence"
Semi-automatic and automatic systems for processing and packaging the beer in bottles, cans or kegs of any size. These plants are made complying with the requirements of craft brewers, opting for solutions able to guarantee reliability in small spaces.
Hermann’s beer filling machine is meticulously designed to seamlessly integrate with the beer production process. Its operational principle involves a systematic procedure: following bottle cleaning, the bottle is conveyed to Hermann’s machine through the bottle feeding belt, then directed to the turntable via the bottle feeding wheel. As the bottle holder ascends, guided by Hermann’s centering device, the bottle mouth is securely sealed beneath the filling valve inlet.
Upon bottle emptying, Hermann’s beer filling machine introduces carbon dioxide (CO2) from the tank into the bottle. When the air pressure inside the bottle equals that of Hermann’s storage tank, the liquid valve opens, propelled by the spring. At this moment, beer flows through the umbrella-shaped reflective ring on Hermann’s return air pipe, filling the bottle along the bottle wall. As the beer reaches a specific height, the filling process halts with precision, ensuring a thorough and controlled filling operation.
Explore further details about our customized solutions and how we can enhance the growth and success of your business with our cutting-edge beer bottling/canning technology solutions.
How to choose a beer-filling machine
Bottling Requirements for Your Brewery
Selecting the appropriate beer filling equipment for your brewery begins with a thorough understanding of your filling requirements.
Questions to consider include:
1. Production Rate: How many bottles or cans do you need to fill per hour?
2. Container Specifications:What are the size and shape of your containers?
3. Carbonation: Do you need to fill carbonated or non-carbonated beer?
4.Sterilization and disinfection
These factors play a crucial role in choosing the equipment that aligns perfectly with your brewery’s production goals and the characteristics of your beer products.
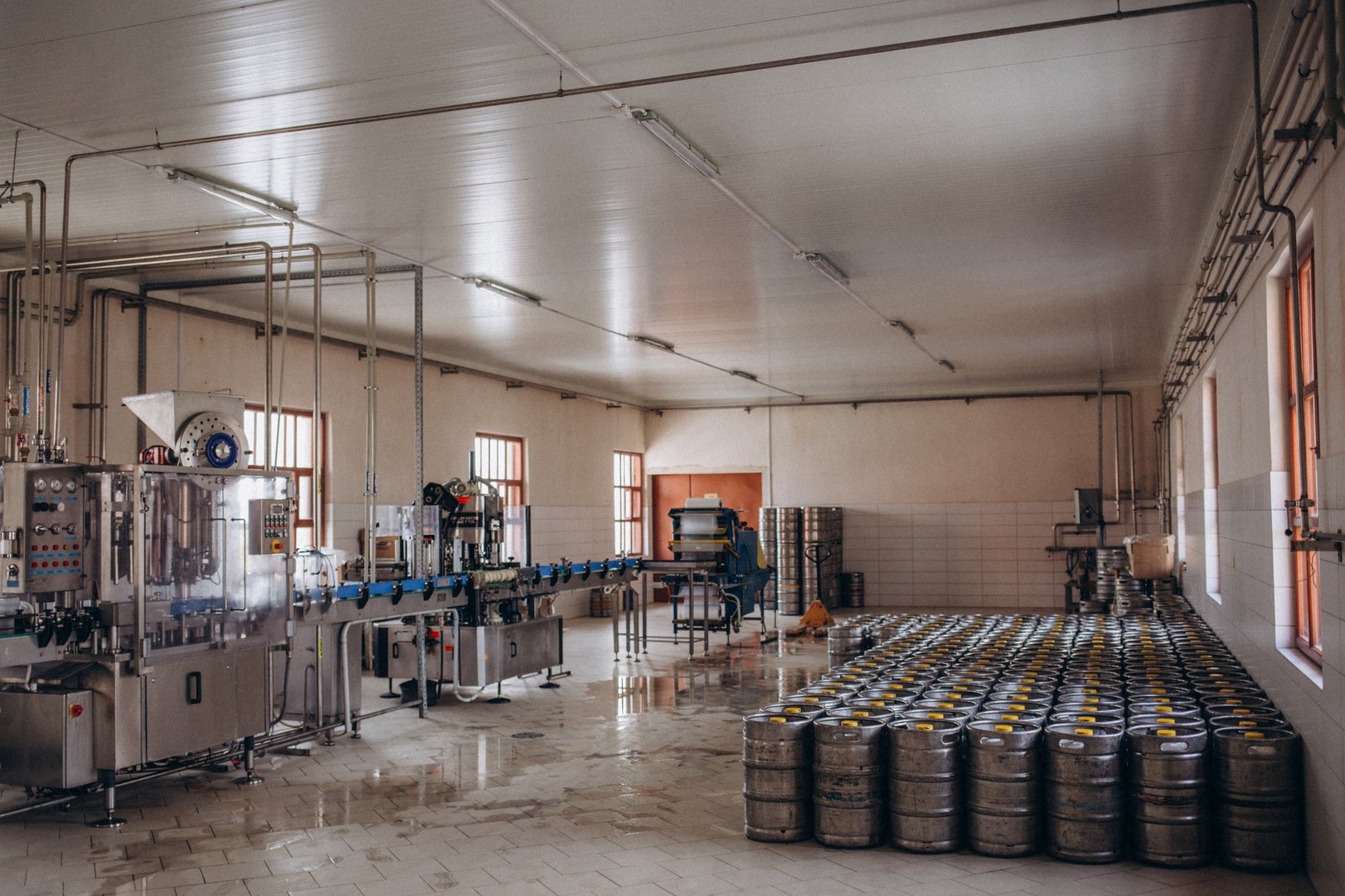
How Many Types of Beer Filling Equipment Are There?
There are four main types of beer filling equipment: counter-pressure fillers, gravity fillers, isobaric fillers, and piston fillers. Each type possesses distinctive features and advantages, catering to specific brewery needs and production requirements.
Counter Pressure Fillers: Widely adopted in the brewing industry, counter pressure fillers employ CO2 pressurization to efficiently fill both bottles and cans with carbonated beer. Their versatility makes them a popular choice for various packaging formats.
Gravity Fillers: Operated by the force of gravity, these fillers may have a slower pace, but they prove highly effective, especially when filling non-carbonated beer. Their simplicity and reliability make them suitable for specific brewery requirements.
Isobaric Fillers: Adding an extra layer of precision, isobaric fillers utilize a vacuum alongside CO2 pressure to ensure the even distribution of carbonated beer in both bottles and cans. This technology contributes to consistent product quality.
Piston Fillers: While operating at a slightly slower speed, piston fillers shine in filling thicker liquids such as stouts and porters. Their piston mechanism accommodates a range of beer viscosities, providing versatility in the brewing process.